SIEMENS ENCODERS IN INDIA
We distribute Siemens Encoders in Chennai, Bangalore, Pune, Mumbai, Ahmedabad, Hyderabad and Delhi.
Industrial Direct India is a leading dealer and distributor of Delta Encoders in India.
Siemens encoders are a vital component in the field of automation and industrial control systems, providing reliable and precise measurement of rotational position and speed. These devices play an essential role in various industries such as manufacturing, robotics, automotive, and packaging, ensuring high performance in machinery and processes.
Our range of Siemens Encoders can offer ingress protection up to IP68 for extreme harsh conditions including ATEX approved for oil rigs and shipping. Also stainless steel for food products. BESPOKE sealing available to combat specific chemicals etc.
Applications of Siemens Encoders
Siemens encoders are used in a variety of applications across multiple industries:
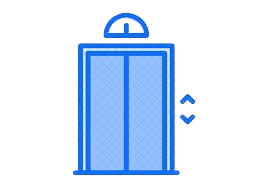
Elevators and Escalators
- Ensuring precise positioning and smooth operation
- They also contribute to the precise stopping at each floor and improve the overall energy efficiency of the lift system.

CNC Machines
- Accurate position measurement for milling, turning, and other machining processes.
- These encoders enable CNC machines to achieve high precision in cutting and shaping materials.

Automation
- Siemens encoders are widely used in motion control systems to provide precise feedback for the positioning of actuators, motors, and robotic arms.
- For feedback in positioning systems and robotic arms.

Conveyor Systems
Speed and position control in material handling and packaging lines.
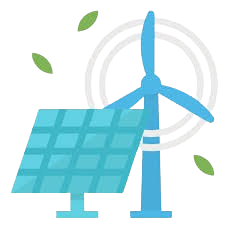
Wind Turbines
- Providing position feedback for blade angle adjustment.
- Siemens encoders provide critical feedback to adjust the blade pitch and turbine orientation for optimal energy generation.
Key Features of Siemens Encoders
Durability
Built for long-lasting operation, Siemens encoders offer extended service life, reducing maintenance needs and improving overall system uptime.
Compact and Versatile
Siemens encoders come in a range of sizes and configurations, ensuring that they can be integrated into both compact and large machinery.
Wide Range of Interfaces
Siemens encoders are available with different output interfaces such as TTL, HTL, or fieldbus options, enabling easy integration with various control systems.
Robust Design
These encoders are designed to withstand harsh industrial environments, with features like IP65 or higher protection, making them resistant to dust, moisture, and vibrations.
High Precision
Siemens encoders offer high-resolution outputs, ensuring accurate and dependable position and speed feedback.
SIEMENS ENCODERS – Linear Encoders
Siemens linear encoders are precision devices designed to measure the position and displacement of objects along a straight line. They are a key component in systems requiring high accuracy and reliability in applications where linear movement needs to be tracked with extreme precision.
Applications of SIEMENS ENCODERS – Linear Encoders
Semiconductor manufacturing
Robotics
Automation
Machine tools
Specification
Operating Temperature : Ranges from -10°C to +70°C (depending on the model)
Power Supply : Typically 5V, 12V, or 24V DC, depending on the encoder model
Environmental Protection : IP65, IP67, or higher, providing protection against dust and moisture
Speed : High-speed capability, typically up to 20 m/s, depending on the model
Accuracy : Typically up to ± 1 µm (micrometer), with high precision in linear positioning
Output Signal : Digital (e.g., TTL, HTL), Analog, or Fieldbus (SSI, Profibus, Ethernet)
Measuring Length : Available in various ranges, from a few millimeters up to several meters
Resolution : Up to 1 nm (nanometer), offering high precision in position measurement
Type of Encoder : Optical, Magnetic, or Inductive depending on the model
SIEMENS ENCODERS – Rotary Encoders
Siemens rotary encoders are precision devices used to measure the rotational position, speed, and direction of rotating objects. These encoders are essential components in various automation and control systems, offering reliable feedback in applications ranging from motor control to robotics and industrial machinery.
Siemens rotary encoders provide high-accuracy measurements in both incremental and absolute configurations, ensuring smooth and accurate motion control across a wide range of industries.
Application of SIEMENS ENCODERS – Rotary Encoders
Motor Control
CNC Machines
Robotics
Conveyor Systems
Elevator and Lift Systems
Specification
Operating Temperature : Ranges from -40°C to +85°C, depending on the model
Environmental Protection : Up to IP67, providing protection against dust, moisture, and harsh conditions
Speed : Can support speeds up to 12,000 RPM or more, depending on the encoder type
Accuracy : Typically ± 0.01° or better, depending on the model and application
Output Signal : Digital (e.g., TTL, HTL), Absolute (SSI, Profibus, EtherCAT, CANopen, etc.)
Measuring Range : 360° rotation for single-turn, multiple rotations for multi-turn encoders
Resolution : Up to 16-bit or higher (65536 positions per revolution or more)
Type of Encoder : Incremental, Absolute, Multi-turn, Single-turn
SIEMENS ENCODERS – Optical Encoders
Siemens optical encoders are high-precision devices designed to measure the rotational position, speed, and direction of mechanical components using optical sensing technology.
Siemens optical encoders are high-precision devices designed to measure the rotational position, speed, and direction of mechanical components using optical sensing technology.
Applications of SIEMENS ENCODERS – Optical Encoders
Robotics
CNC Machines
Semiconductor Manufacturing
Industrial Automation
Medical Equipment
Specification
Power Supply : 5V, 12V, or 24V DC, depending on the encoder model
Operating Temperature : Typically -10°C to +70°C, depending on the specific model
Environmental Protection : IP64, IP67, or higher, providing protection against dust, moisture, and harsh conditions
Speed : Can support rotational speeds up to 12,000 RPM or more, depending on the model
Speed Range Can handle speeds up to 12,000 RPM, making it suitable for high-speed applications.
Accuracy : Typically ±0.01° or better depending on the model and application
Output Signal : Digital (e.g., TTL, HTL), Absolute (SSI, Profibus, Ethernet, CANopen)
Resolution : Up to 24-bit, offering extremely high precision with fine angular increments
Type of Encoder : Incremental, Absolute, Multi-turn, Single-turn
SIEMENS ENCODERS – Incremental Encoders
Siemens incremental encoders are essential components used to measure the rotational position, speed, and direction of a rotating object. These encoders operate by generating a series of electrical pulses as the shaft rotates.
The number of pulses is proportional to the angle of rotation, providing real-time position feedback.
Application of SIEMENS ENCODERS – Incremental Encoders
Motor Control
CNC Machines
Conveyor Systems
Elevator and Lift Systems
Robotics
Specification
Power Supply : 5V, 12V, or 24V DC depending on the encoder model
Mechanical Life : Typically 100 million revolutions or more, offering long-term reliability
Operating Temperature : Ranges from -10°C to +70°C (depending on the model)
Environmental Protection : IP64, IP67, or higher for dust and moisture protection
Speed : High-speed capabilities, up to 12,000 RPM or more, depending on the model
Accuracy : Typically ±0.01° or better, depending on the model
Output Signal : TTL, HTL, Differential, Open Collector
Type of Encoder : Incremental (Rotary, Linear, Shaft Mounted, Hollow Shaft)
SIEMENS ENCODERS – Motor Encoder
Siemens motor encoders are specialized devices designed to provide precise feedback on the rotational position, speed, and direction of motors in various industrial applications. These encoders are integral to motor control systems, enabling accurate speed regulation, torque control, and smooth motion in electric motors.
Applications of SIEMENS ENCODERS – Motor Encoder
Robotics
CNC Machines
Elevator and Escalator Systems
Industrial Automation
HVAC Systems
Specification
Power Supply : 5V, 12V, 24V DC depending on the model
Operating Temperature : Typically -40°C to +85°C, depending on the model
Environmental Protection : IP65, IP67, or higher for protection against dust, moisture, and vibrations
Speed : High-speed capability, up to 12,000 RPM or more, depending on the model
Accuracy : Typically ±0.01° or better depending on the model
Output Signal : TTL, HTL, Analog, SSI, Profibus, EtherCAT, CANopen, or Fieldbus interfaces
Resolution : Typically up to 10,000 pulses per revolution (PPR) or higher
Type of Encoder : Incremental, Absolute, Multiturn, Single-turn
SIEMENS ENCODERS – Absolute Encoders
Siemens absolute encoders are high-precision devices used to measure the rotational position of a shaft or object, providing unique position feedback for each angle of rotation. Unlike incremental encoders, which only measure relative position, absolute encoders maintain a constant, unique position reading even after power loss.
This makes them ideal for applications that require continuous and reliable position data without the need for recalibration after shutdowns.
Application of SIEMENS ENCODERS – Absolute Encoders
Medical Equipment
CNC Machines
Industrial Automation
Elevator and Lift Systems
Robotics
Specification
Power Supply : 5V, 12V, or 24V DC depending on the model
Operating Temperature : Typically -40°C to +85°C, depending on the model
Environmental Protection : IP65, IP67, or higher for protection against dust, moisture, and contaminants
Speed : High-speed capability, up to several thousand RPM, depending on the model
Accuracy : Typically ±0.01° or better, depending on the model
Output Signal : SSI (Synchronous Serial Interface), Profibus, Ethernet/IP, EtherCAT, CANopen
Resolution : Typically 12-bit to 30-bit, depending on the model
Type of Encoder : Single-turn, Multi-turn, Optical, Magnetic
FAQ
What output signals do Siemens encoders support?
Siemens encoders support a wide range of output signals, including:
- TTL (Transistor-Transistor Logic)
- HTL (High Threshold Logic)
- Analog Signals
- SSI (Synchronous Serial Interface)
- Fieldbus Protocols such as Profibus, EtherCAT, CANopen, and Ethernet/IP
How do I choose the right Siemens encoder for my application?
Choosing the right Siemens encoder depends on several factors, including:
- Type of movement (rotary, linear, motor control)
- Resolution requirements
- Environmental conditions (dust, moisture, temperature)
- Power supply requirements
- Communication interface compatibility with your control system Consult Siemens documentation or a Siemens distributor to ensure the encoder meets your specific application needs.
How do Siemens encoders communicate with other devices?
Siemens encoders communicate with other devices, such as PLCs (Programmable Logic Controllers), motor controllers, and automation systems, using various communication protocols. Common communication protocols include SSI, Profibus, EtherCAT, and CANopen, ensuring seamless integration with industrial control systems.