SCHNEIDER ENCODERS IN INDIA
We distribute Schneider Encoders in Chennai, Bangalore, Pune, Mumbai, Ahmedabad, Hyderabad and Delhi.
Schneider Electric, a global leader in energy management and automation, offers a comprehensive range of encoders designed to provide high-precision feedback in a wide variety of industrial applications. Encoders play a crucial role in motion control systems by converting mechanical motion into an electrical signal, which can be used for position, speed, and direction sensing.
The graphic below outlines the basic construction of an incremental rotary encoder using optical technology. A beam of light emitted from an LED passes through the Code Disk, which is patterned with opaque lines (much like the spokes on a bike wheel). As the encoder shaft rotates, the light beam from the LED is interrupted by the opaque lines on the Code Disk before being picked up by the Photodetector Assembly. This produces a pulse signal: light = on; no light = off. The signal is sent to the counter or controller, which will then send the signal to produce the desired function.
Applications of Schneider Encoders
Schneider encoders are used in a variety of applications across multiple industries:

Robotics
Schneider encoders play a vital role in robotics by providing real-time feedback on the position and speed of robotic arms and joints. This ensures that robots perform tasks such as assembly, welding, and packaging with high precision.

CNC Machines
In CNC (Computer Numerical Control) machines, encoders provide feedback on the position of cutting tools, enabling precise machining of metals, plastics, and other materials.

Industrial Automation
Encoders are essential in industrial automation systems for controlling and monitoring machinery, motors, and robotic arms. They help ensure precise positioning and movement for conveyor belts, assembly lines, and automated processes.

Packing Machine
Encoders are integral to packaging machinery, ensuring that products are correctly aligned, placed, and packed with minimal errors.
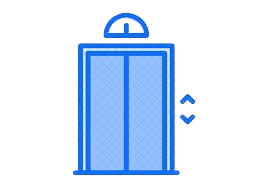
Elevators and Escalators
Encoders from Schneider Electric are used in elevator and escalator systems to provide feedback on motor position and speed, ensuring smooth and safe operations.
Key Features of Schneider Encoders
Compact and Flexible Design:
Schneider encoders come in a variety of compact sizes and mounting options, making them suitable for applications where space is limited.
High-Speed Performance
Schneider encoders are capable of operating at high speeds, with some models supporting speeds up to 12,000 RPM or higher. This makes them ideal for fast-moving applications such as robotics, CNC machines, and high-speed production lines.
Durability
Designed for use in harsh industrial environments, Schneider encoders offer robust protection against dust, moisture, and temperature extremes. Many models come with protection ratings such as IP65 or IP67, ensuring reliable operation even in tough conditions.
Versatile Communication Options
chneider encoders provide a wide range of communication interfaces, including SSI (Synchronous Serial Interface), Profibus, EtherCAT, CANopen, and more. This ensures seamless integration into automation systems and industrial networks.
Precision and Accuracy
Schneider encoders offer high-resolution feedback, ensuring precise measurement of position, speed, and direction. With resolutions ranging from hundreds to thousands of pulses per revolution (PPR) for incremental encoders, and up to 30-bit resolution for absolute encoders, Schneider encoders cater to various levels of accuracy required by industrial applications.
SCHNEIDER ENCODERS – Opto-electronic rotary encoders
Schneider Electric offers a range of Opto-Electronic Rotary Encoders, known for their high precision, durability, and versatility in various industrial applications. These encoders are designed to measure the rotational position, speed, and direction of a rotating object, converting mechanical movement into a digital signal that can be used for real-time monitoring and control.
Schneider’s opto-electronic rotary encoders leverage optical sensing technology to provide highly accurate feedback, making them an ideal choice for industries that demand high-performance motion control systems.
Applications of SCHNEIDER ENCODERS – Opto-electronic rotary encoders
Conveyor Systems
Robotics
Automation
Printing Shops
Continuous Processes
Material Handling
Cutting Machines
Cranes
Specification
Supply Voltage : Wide supply voltage options, including 5V DC and 24V DC for compatibility with different control systems.
Speed Range : Can operate at speeds up to 12,000 RPM or higher, ideal for high-speed applications.
Shaft Diameter : Shaft sizes ranging from 6 mm to 15 mm to accommodate various motor types.
Operating Temperature Range : Typically from -40°C to +85°C, suitable for use in extreme industrial conditions.
Protection Class : Encoders are available with IP65, IP67, or higher protection ratings for harsh environments.
Output Signal : Options include TTL, HTL, Differential signals, and various fieldbus protocols.
Resolution : Resolutions from 100 PPR (Pulses Per Revolution) to 10,000 PPR for precise feedback.
Encoder : Type Available in Incremental, Absolute, Rotary, Linear, and Optical types.
FAQ
Why choose Schneider Encoders?
Schneider encoders offer high precision, reliability, and durability, designed to meet the needs of demanding industrial applications.
How do I choose the right encoder for my application?
The choice of encoder depends on factors such as the type of machinery, required precision, and environmental conditions. Our team can assist you in selecting the ideal encoder for your needs.